
HYScale technology
The HYScale technology results from intense research and development within multiple projects, such as the EU-funded projects NEWELY, Anione, and ECO2Fuel, It is based on the anion exchange membrane water electrolysis (AEMWE) technology.
Due to its many advantages, the HYScale technology is well suited to become the future electrolyser technology delivering economical and truly green hydrogen.
With an estimated CAPEX of €400 per kilowatt at the system level, it will use:
- critical raw material-free catalysts,
- fluorine-free anion exchange membranes and catalyst ionomeric binder,
- diluted KOH concentration (< 1 molar KOH)
The innovative components in the HYScale electrolyser stack enable it to operate at a high current density, 2.9 times greater than the current state of the art. This scalability potential – with active surface areas exceeding 400 cm² – positions HYScale to uphold the EU’s leadership in water electrolysis technologies.
Disadvantages of SoA electrolyser technologies
- High CAPEX (PEMWE & AWE),
- Use of critical raw materials (PEMWE mainly),
- Large land footprint (AWE),
- Complex cell/stack design (PEMWE),
- Highly corrosive electrolyte (AWE),
- Need for ultra-pure water (PEMWE).
It’s also due to these reasons that hydrogen production cannot be achieved more cost-effectively with the PEMWE and AWE.
HYScale advantages
The use of anions exchange for water electrolysis needs to possess:
- High hydroxide ion conductivity,
- Mechanical and chemical stability,
- Consistent quality in terms of batch-to-batch reproducibility,
- Low hydrogen and oxygen crossover.
These tests were done at a current density of 1 A·cm⁻², being only a minor improvement compared to the already mature and widely used alkaline water electrolysis (AWE) with an operational capacity of 0.6 A·cm⁻². It doesn’t appear that the AIE degradation is improving neither. Considering the consistency of the batch-to-batch quality, the AEMs failed to maintain the same performance from batch to batch.
This is due to the water-sensitive and complex chemistry and the need for all chemistries to be performed under an inert atmosphere. As a conclusion, less complex synthesis routes need to be developed.
Anion exchange membranes and ionomers
- Flexibility: the membranes exhibit exceptional flexibility in both dry and wet states, simplifying stack assembly processes.
- High conductivity and stability: achieved through an innovative nanophase separation technique in synthesis, forming conductive channels that allow efficient ion transport.
- Cost-effectiveness: both the ionomer and the membrane are produced from the same batch, reducing production time and costs.
Electrodes upscaling
The upscaling process of the electrodes in the HYScale project is a critical step towards achieving a final electrolysis stack with a 400 cm² surface area, designed to be both efficient and scalable for future industrial-level production.
This process is strategically divided into distinct phases, ensuring that each aspect of the technology is enhanced for optimal performance and sustainability.
Key aspects of the upscaling process include:
- Catalyst ink upscaling: enhancing the formulation and production of catalyst ink for improved efficiency.
- Catalyst application technique: refining the methods used to apply the catalyst, ensuring uniformity and effectiveness.
- PTL production with reduced nickel: focusing on reducing the nickel content in the PTL to address future material scarcity concerns.
Stack design
At the core of the HYScale stack design is the ability to operate at a high current density of 2 A×cm⁻², which significantly lowers the capital costs (CAPEX). This is a crucial development in the electrolysis field, where efficiency and cost reduction are paramount.
The stack’s design marries the advantages of PEM and alkaline electrolysis, enabling the use of thin anion exchange membranes (AEMs) and ionomers. This allows for efficient stack sealing and better overall performance, operating effectively at the mentioned high current densities.
What makes HYScale’s stack design truly stand out is its strategic configuration, which includes:
- Economic Porous Transport Layers (PTLs): these are carefully chosen to ensure cost-effectiveness while maintaining high performance.
- Economic Bipolar Plates (BPP): selected for their high conductivity and good corrosion resistance, these plates are especially suited for AEM water electrolysis, which operates in low-concentration KOH solutions. This choice also mitigates issues with high-concentration alkaline solutions that typically affect the BPP durability.
- Flow field designs: by adopting a novel design, HYScale’s stack can be scaled to large sizes without a proportional increase in costs.
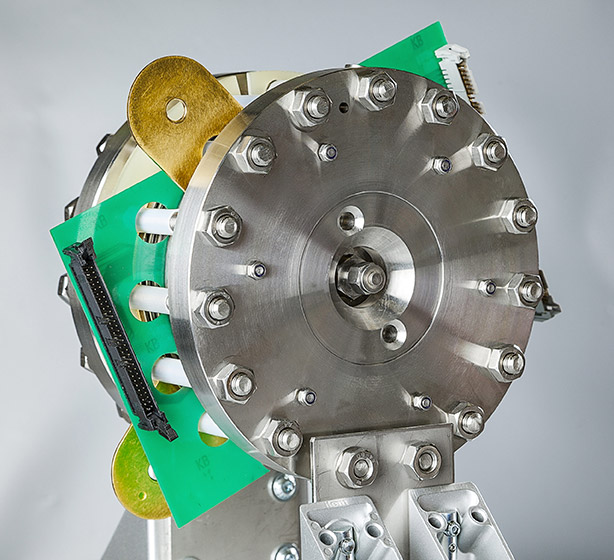
The stack design also uses a novel approach to managing the KOH concentration, feeding the cells with very diluted solutions, which simplifies auxiliary processes and minimises the risk of corrosion. This attention to detail in the design phase underpins the project’s goal to deliver not only an efficient but also a scalable and durable solution for hydrogen production. The stack’s configuration and the choice of materials reflect a deep understanding of the challenges and requirements of modern electrolysis systems, ensuring HYScale’s position at the forefront of electrolyser innovation.
Backed up by EU-funded research
NEWELY
NEWELY is a new prototype of Anion Exchange Membrane Water Electrolysers (AEMWE) characterised by a high-performance, cost-effectiveness and durability.
The 2 kW 5-cell AEMWE stack prototype is based on hydraulic compression with novel components characterised by superior performance and stability. It is fed with pure water feedstock at a temperature of at least 45°C and it keeps this performance for 2,000 hours.
More on https://newely.eu
ANIONE
ANIONE technology will allow for scalable, efficient and low-cost production of green hydrogen from a variety of renewable energy sources. The wide-scale production of hydrogen will enable large-scale applications in grid balancing markets, in power-to-gas storage systems, and in the sustainable transport and mobility sector.
More on https://anione.eu
ECO2Fuel
ECO2Fuel aims to design, manufacture, operate, and validate the worldwide first low-temperature 1MW direct, electrochemical CO2 conversion system to produce economic and sustainable e-fuels and chemicals.
More on https://eco2fuel-project.eu/